Integrating work into the design: The case of offshore maintenance
Abstract
BACKGROUND:
Ergonomics in design is intended to close the gap between what is designed and the real work. This study discusses the creation of technical ergonomics requirements for the basic design stage of workshops on offshore platforms.
OBJECTIVE:
This paper intends to show how the ergonomics discipline contributes to integrating knowledge on the real work of the maintenance crew with the design.
METHODS:
This case study uses procedures, data collection, and analysis guided by the Ergonomics of the Activity’s (EA) theoretical framework, focused on design projects.
RESULTS:
The results show how ergonomics contributed to a better understanding of maintenance work, as well as how this knowledge was integrated into the project design. This occurred both through the construction of a new layout and equipment list, and through the development of technical specifications. These products enable greater operational efficiency, reductions in the costs of alterations in the next stages of the project, and improvement in working conditions.
CONCLUSIONS:
This work points to the need for new studies on platform maintenance work, in addition to studies that deepen the debate on consolidating ergonomics practice in design projects.
1Introduction
Most ergonomics actions in companies are still restricted to anthropometric and physiological data. It is common to come across the lack of knowledge about ergonomics practice in a design situation [1–3]. Therefore, many times ergonomists are requested to act only to furniture heights, parameters for chairs purchasing, among others. In these cases, knowledge about work is not effectively incorporated into projects. Whereas, Ergonomic Work Analysis (EWA) is an efficient approach in recovering operational experience for the construction of design parameters [1, 4]. This approach studies the activity from the observation of the worker in real work situations.
The design process of oil platforms has a specific organization, often guided by technology-centered criteria [4, 5]. And one of the difficulties identified in design projects is the gap between what is designed and the crews’ real work [1]. This is the hiatus in which ergonomics can be inserted as a design discipline.
In projects of continuous process industry, Ergonomics and Engineering can be complementary, acting together in the technological development process [6]. According to Duarte [6], the anticipation of future problems based on knowledge of real work has become a strategic dimension. For ergonomics, the main object of analysis and questioning is the activity, from which the ergonomist validates his action [1].
This study is based on the ergonomics team’s participation in the basic design of new offshore platforms [7, 8]. At this stage of the project, the creation of technical specifications for the hull and topside areas of the platform were directed to ergonomics. An earlier version of this paper appeared in Mercado et al. [7].
This creation of ergonomics technical specifications involves challenges, such as transforming knowledge about real work into information that can be used by designers [6, 9–12]. According to Conceição et al. [10], technical specifications can be considered an intermediary interface between designers and knowledge about usage.
The purpose of this paper is to show and discuss the creation process of technical ergonomic requirements for workshops. In this context, this study also intends to show how the discipline of ergonomics integrated knowledge on the maintenance crew’s real work into the technical documents.
2Method
This research consists of a case study of qualitative and exploratory approach with procedures for data collection and analysis guided by the theoretical framework of the Ergonomics of the Activity [1, 2, 13] focused on design projects.
For this theoretical framework work analysis was performed in reference situations, which are work situations that present functions or characteristics similar to those desirable in the future project [1, 14]. This framework also proposes the use of intermediate objects to assist in the communication, anticipation of results, and recording the history of project decisions [10, 15].
The following stages were carried out to meet the proposition of the theoretical background [13]: a) demand analysis; b) analysis of the organizational, technical, economic, and social environmental aspects; c) analysis of the work activities in the reference situations; and d) validation of the study and recommendations to improve the work.
The survey was conducted in a Brazilian energy company from 2018 to 2020 [7, 8]. Ethical procedures that guide ergonomics practice and follow the code of ethics established by the Brazilian Association of Ergonomics [16] were used, and the following precautions were taken:
- Research subjects were previously informed about the study and agreed to their participation,
- The company’s management formally authorized the study, and
- Names and certain information were kept confidential and not reported.
The data was analyzed using primary and secondary sources of record. The primary source analysis was based on project records and notes from reference situations analysis. The project records contain minutes of internal and external meetings, as well as notes on project development and interviews with basic design stage designers. In parallel, the reference situations records include notes about on board work and interviews with workers. To complement, the secondary source analysis refers to the Brazilian regulatory standards, the company’s data regarding the reference situations and the project, and the ergonomic analysis reports of previous projects. These analyses allowed the participation in technical discussions with the project disciplines and the development of documents.
The data provided by the company were: technical specifications of other disciplines, basic design reports and guidelines, equipment list, blueprints, reports of other reference situations, descriptive memorials, and checklists for design review. Also, the data provided by reference situations included: description of the maritime unit, description of accidents, organization charts, and People on Board list (POB).
For the integration of the knowledge of real work into the new platforms design, the researchers of this work participated directly in the creation of specifications. Several meetings were held to develop the design and create the specifications, among which five were exclusively aimed to discuss workshop documents such as layout, equipment list, and technical specifications. These meetings were held with representatives of the architecture, operation, and maintenance teams, among others.
The first one took place before the first visit to the reference situations and was attended by the ergonomics team (including the researchers and company ergonomists), the architecture team, and platform maintenance supervisors. The architecture team presented the workshop equipment list and updated layout (digital and printed) for the design discussion at that meeting. As a follow-up, a new version of the workshop equipment list and layout was issued. Subsequent meetings were interspersed with visits to reference situations.
Besides these meetings with specific themes, other moments of interaction with designers also contributed to exchanging knowledge and information on the maintenance crew’s work, such as the Design Review (DR) event and other periodic meetings. In both meetings and DR sessions, intermediate objects were used, such as 2D plans (printed and digital), workshop equipment lists, and the 3D model.
2.1Analysis in the reference situations
For the work activity analysis in the platform’s different environments, 12 visits were made to the 4 platforms selected as reference situations, as shown in Table 1. The platforms were selected because they have characteristics similar to the future project. This paper will only cover data relating to the activities of maintenance crews.
Table 1
Visits made in reference situations
Reference situation | Visit period |
Platform A | November 2 to 4, 2018 |
Platform B | May 17 to 20, 2019 |
Platform B | July 8 to 11, 2019 |
Platform A | July 19 to 21, 2019 |
Platform A | August 8 to 11, 2019 |
Platform A | September 3 to 6, 2019 |
Platform B | September 2 to 6, 2019 |
Platform B | November 11 to 14, 2019 |
Platform C | December 8 to 15, 2019 |
Platform C | January 12 to 16, 2020 |
Platform A | March 7 to 10, 2020 |
Platform D | March 14 to 17, 2020 |
Source: Authors (2021).
Pre-boarding meetings were conducted before each visit. Such meetings were held via videoconference with the onshore manager and offshore leadership. The objectives were to collect information about the current operation of the unit, to request unit documents, and to present the researchers’ action plan to the leadership.
As guided by the EWA methodology, during the initial visits, researchers seek to understand the general operation of the unit and of the platform maintenance workshops. As the studies progressed, the most critical aspects were selected for discussion, from which more detailed investigations were developed. This process took into account the necessary changes for the design of the future installation.
In general, the visits to reference situations included: interviews with maintenance supervisors and coordinators, participation in daily safety meetings and shift changes, and analysis of maintenance team’s activities, both within and outside workshops.
In addition, during visits to the workshops, the following intermediate objects were used: blueprints of the basic design workshops (in A3 format) and equipment list.
In the first visit to a reference situation, an analysis of the general operation of the unit was conducted, including a visit to workshops and maintenance teams. Interviews were conducted with the platform manager, coordinators, supervisors and maintenance technicians. In the second visit, besides interviews with maintenance technicians about typical work situations, the workshop blueprints and the list of equipment were used as intermediary objects for discussion with these workers.
After the second visit, collected information was discussed internally with the ergonomics team. And then, taken to the architecture team (responsible for both layout and maintenance equipment list). In this process, four meetings were held exclusively for treatment of these obtained data onboard. As a result of these meetings, new versions of these documents were generated, which were taken to several subsequent visits to reference situations, in order to be validated with maintenance technicians, coordinators, supervisors from different units and maintenance crews.
In summary, this process generated a constant reformulation of documents. The information was collected, through work observation, interviews, and confrontations with workers, and returned for new meetings. This interchange between field and the design situation, as well as the feedback flow of information supported the design decisions-making process.
As a result of this participation in the project, contributions were generated for the new layout, equipment list and technical specifications, which are presented below.
3Results
The results show how the participation of ergonomics, based on the understanding of the maintenance team’s work, can contribute to the following aspects: reduction of project change costs; increased efficiency in the next stages of the project, improved working conditions for operators of future units.
In this project, specifically, the actions that contributed to this objective included: the creation of ergonomics technical specifications, contributions to technical specifications from other disciplines, definition of new layouts and validation of the equipment list.
3.1Ergonomics technical specifications
Altogether, 50 specifications were created for the workshop chapter of the ergonomics technical specifications document. These specifications can be categorized in 6 main groups (Fig. 1): 6 on initial conditions; 17 on layout, furniture, and equipment of the set of workshops; 12 specific to the mechanical workshop; 7 specific to the instrumentation workshop, 4 specific to the electrical workshop; 3 for the boiler-room; and 1 for the PSV workshop. The details of some of these specifications will be presented as an example.
• Maintenance supervisors’ office
Fig. 1
Type of technical specifications for workshops.
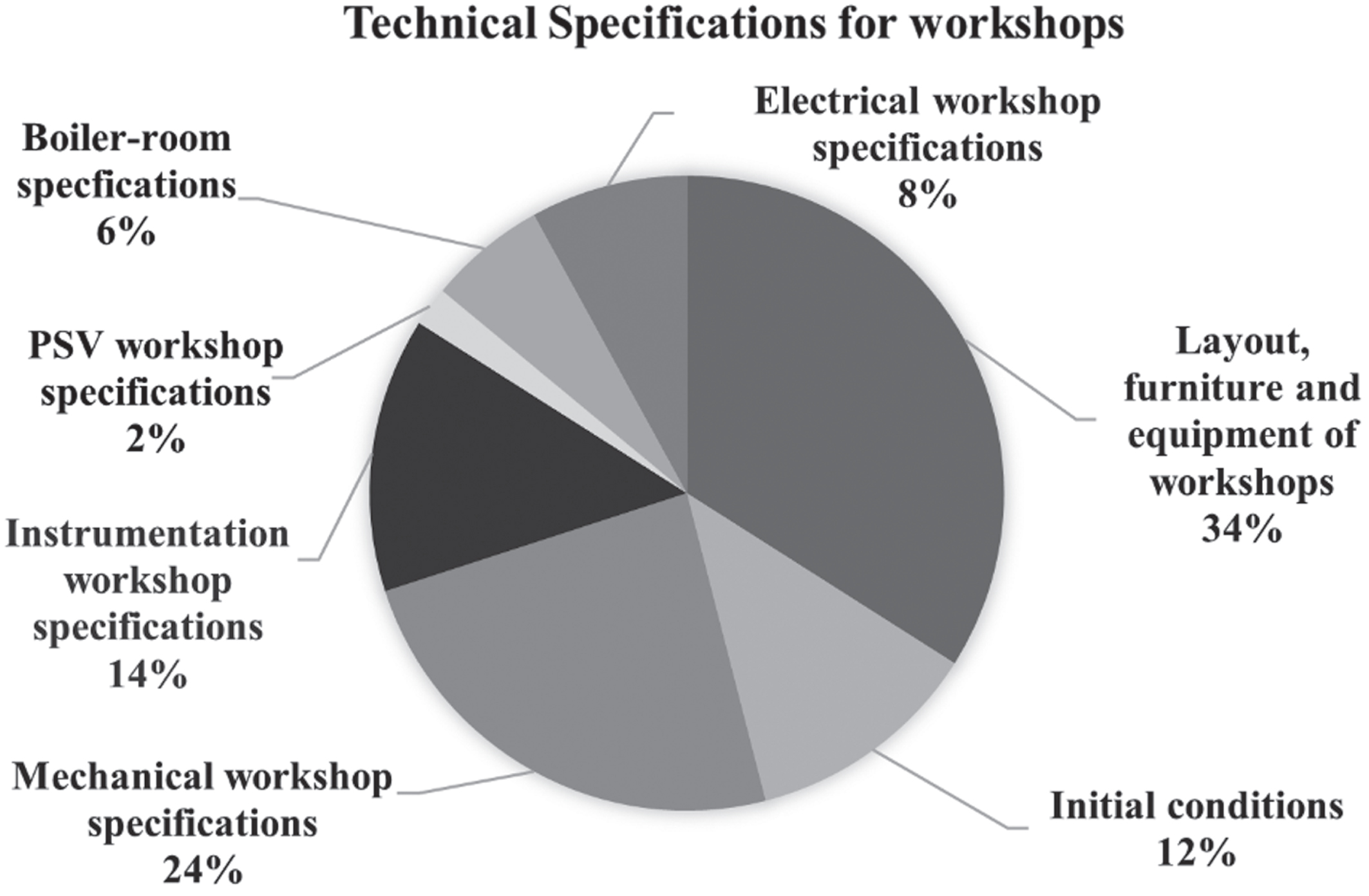
The supervisors’ work routine includes daily checking of the planned services and contacting field operators to issue a work permit.
In the reference situations, mechanical, electrical and instrumentation workshops, as well as the warehouse, are located on the first level of the engine room. They are located close together, but in different environments. In addition to the office environments for supervisors, the workshops have workstations with computers for maintenance technicians to perform administrative activities.
In one of the units, however, it was observed that supervisors do not occupy their offices, located in the workshops. They have their work stations in the main office of the platform, which is located a few levels above the workshops. According to these supervisors, it was a management decision taken in order to integrate all these professionals in the same room, and to facilitate the decision-making process. Nonetheless, they claim that, despite improving communication between leaders from different areas, it makes internal communication with the maintenance teams difficult, as well as the organization of activities with them.
This corroborated the decision to maintain, in the current project, the supervisors’ offices in the workshop environment, close to their respective teams. This proximity favors team decision-making, thus increasing the agility of actions taken and the efficiency and productivity of the platform as a whole.
• Workshops’ location
Reference situations analysis shows that one of the main difficulties observed in the workshops refers to their location. In addition to not having a restroom, they are also difficult to access, especially for frequent displacements and carrying tools. It is necessary to descend two stairs with a steep slope to access the workshop area. This great inclination is due to adaptations generated due to the use of an existing ship for constructing the platform.
As the basic design in progress doesn’t foresee the reuse of another ship hull, it was not necessary to specifically recommend the access stairs for the workshops. Regardless, a recommendation to improve the handrail was reported to the reference situation leadership, with the purpose of reducing the risk of falls.
In the initial conditions of the technical specifications for workshops, it was recommended that workshops, warehouse and tool shop shall be located close to each other, considering the common use of cargo handling resources.
These specifications were inserted in order to contribute to improve the effectiveness of actions in these environments, aiming at better working time efficiency of offshore maintenance teams, in addition to reducing the risk of illnesses generated by excessive displacement, as currently occurs in units in operation.
• Monitoring screens
Upon analyzing the maintenance crew’s work, it was observed that it involves activities beyond just maintenance itself. The crew’s duties include the operation of equipment that guarantee the hull’s operation, such as air conditioning and ventilation systems, water and sewage systems, electrical installations, etc.
Initially, the idea was that the information from these equipment and systems would be monitored by a control room operator - a few levels above the workshops - who should transfer the information to the maintenance team.
However, after the construction of the units, all platforms installed screens (plant information system - PI) in the workshops for monitoring and controlling the equipment / systems that are the responsibility of the maintenance team (Fig. 2).
Fig. 2
Plant information system.
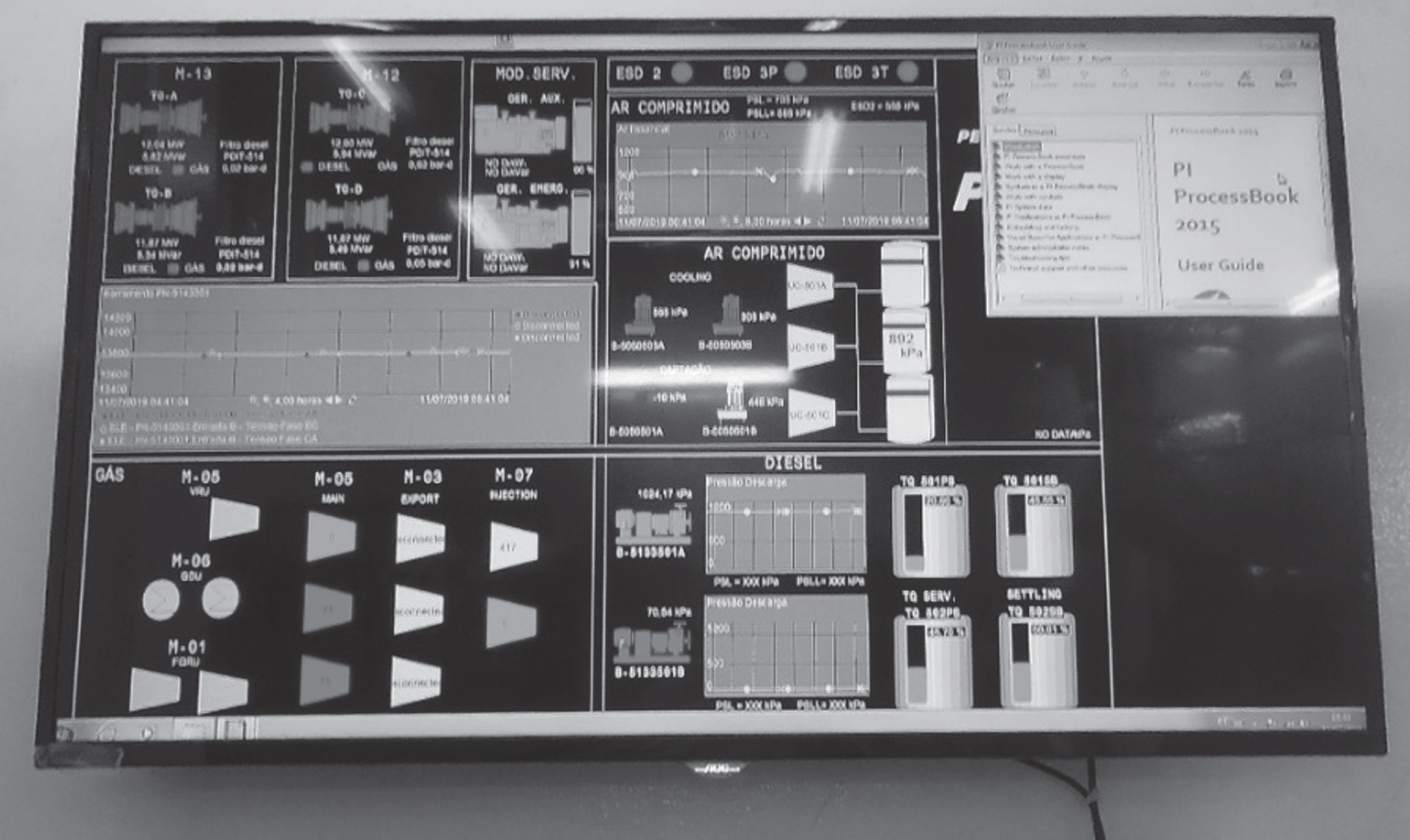
The exhibition of this control system was not foreseen in the project and was improvised by the maintenance operators. Hence, a technical specification was created recommending the installation of screens in the workshops with an equipment monitoring system, such as in the control room. This specification aims to contribute both to greater efficiency and to greater process safety, considering the improvement in the control management of these equipment.
• Support areas for maintenance teams
The analysis of the reference situations highlighted that the activities of the maintenance teams occur both in the workshops and in other areas of the platform. Repair activities that cannot be performed in the process area are conducted in the workshops, which are also used to administrative and system monitoring activities related to filling out reports, scheduling activities, etc.
The ergonomics analysis of maintenance activities led ergonomists to identify difficulties related to the lack of support benches for technicians in the process area. Although some platforms have already installed some benches in specific points of the platform, they still do not have the necessary tools to meet maintenance demands.
Therefore, the workers created the strategy of using an individual backpack with essential tools, so each operator has custody of their tools. This backpack weighs up to 10 kg, so they are exposed to great physical effort due to this load transportation, despite the fact that they have minimized the displacement.
Therefore, in this basic design, it was recommended the supply of support benches (containing basic maintenance tools) in the process area. It was also recommended that workshops were located on the main deck to provide greater flexibility in solving problems and to reduce displacements.
3.2Contributions to other disciplines’ technical specifications
As mentioned in the previous items, in addition to workshops, the maintenance crews also work in other platform areas, such as the battery room.
During the work analysis, it was observed that the type of battery influences the maintenance frequency and, consequently, the access to the battery banks. Thus, the first premise of the design was to consider the type of battery that should be used and, based on this definition, provide sufficient space for its maintenance and operation, such as access for filling and density measurement of the batteries. There should also be space to allow for the movement of trolleys for battery removal and exchange, as well as load handling devices that consider the type of handle, weight, and dimensions of each unit to be exchanged.
The ergonomic specifications for battery rooms are examples of contributions that had to be transferred to the technical specifications of other disciplines due to the bidding process and distribution of documents to the vendors in further stages of the project.
These specifications for battery rooms were inserted in the electric technical documentation, because the work by the contracted company - responsible for the construction and assembly project of the battery room - is based on the electric technical specification.
3.3Definition of new layouts and validation of the equipment list
Regarding layout of the workshops, significant differences were observed among the platforms visited. Those differences included, for instance, the arrangement of equipment, hoist and monorail position, and maintenance workbenches aspects, as described below.
One of the units had a larger workbench compared to the others, which facilitated the maintenance activities. Furthermore, its location was central in the workshop space, which allowed more than one worker to work simultaneously on it and favored the placement of equipment and parts on it.
In other units, the benches were positioned against the bulkhead (Fig. 3), and the technicians needed to move the equipment on the workbench to repair it.
Fig. 3
Bench against the bulkhead.
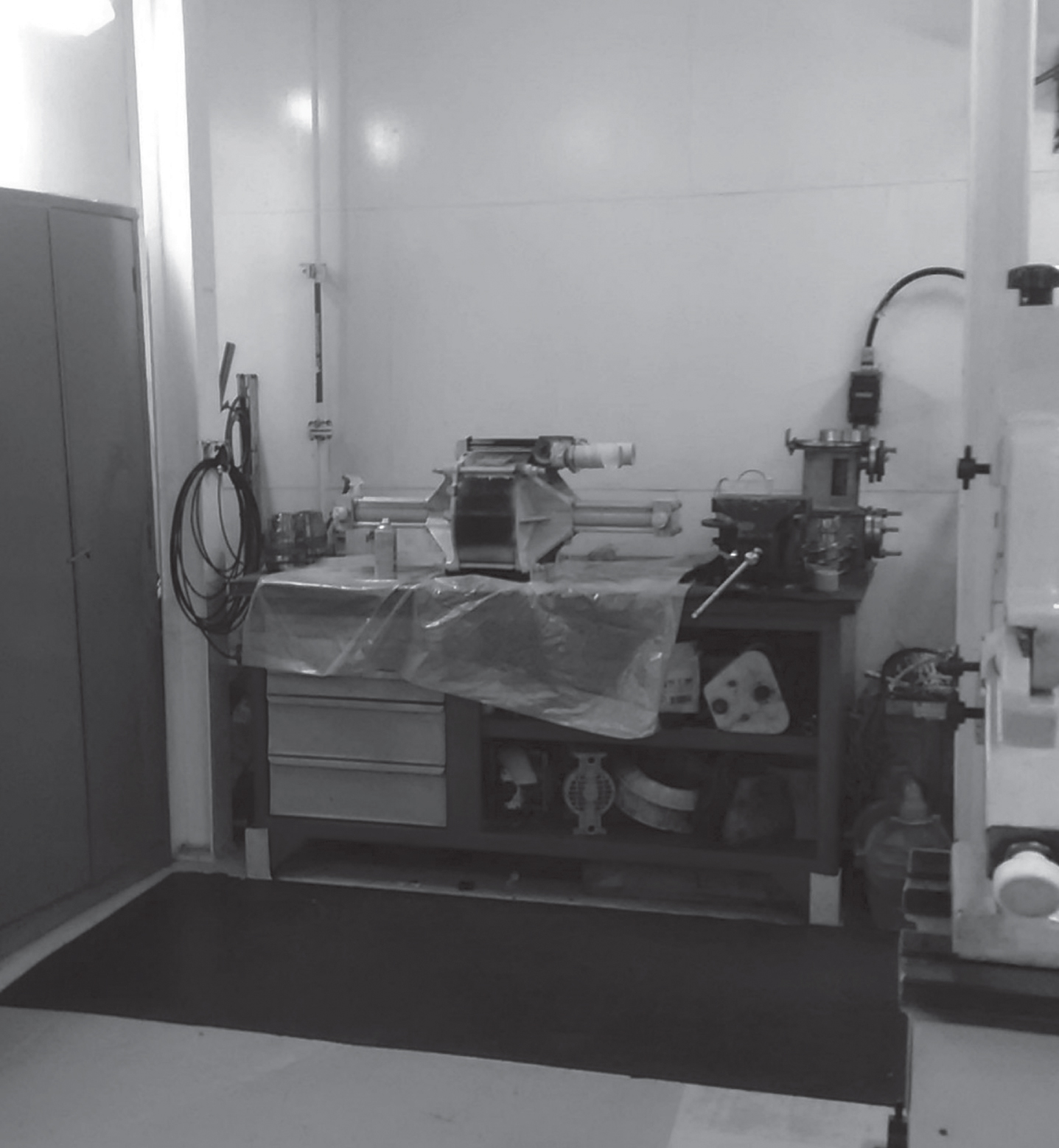
In relation to the equipment arrangement, the mechanical lathe of some reference situations was not positioned aligned to the monorail track. This arrangement makes the cargo handling activity difficult, or even impossible in certain cases. The equipment proximity, both in relation to each other or to the bulkhead, results in difficulties for technicians to repair large and/or heavy parts in these machines.
The difficulties arising from the positioning of the equipment influence the performance of the team’s work, impacting the following aspects: the quality of the final service; task execution time and staff availability; and risk of accidents.
In another unit, it was observed that there were two presses located in the mechanical workshop, one being a hydraulic press and the other, an electric one. The electric press was positioned close to the bulkhead and shelf, in a way that made it impossible to carry out the activity. Therefore, only the hydraulic press is used, although they have reported that the electric one has better performance.
As a result, the specification created concerned the physical arrangement of workshop equipment. Thus, it was specified that the equipment’s positioning must consider the size of the parts that will be used on them, and therefore, equipment must be at a minimum distance of 1 m from any obstacles.
Also, it has been noted that in one of the units the hoist of the maintenance workshop is disproportionate to the workbench (Fig. 4).
Fig. 4
Disproportionate hoist to the workbench.
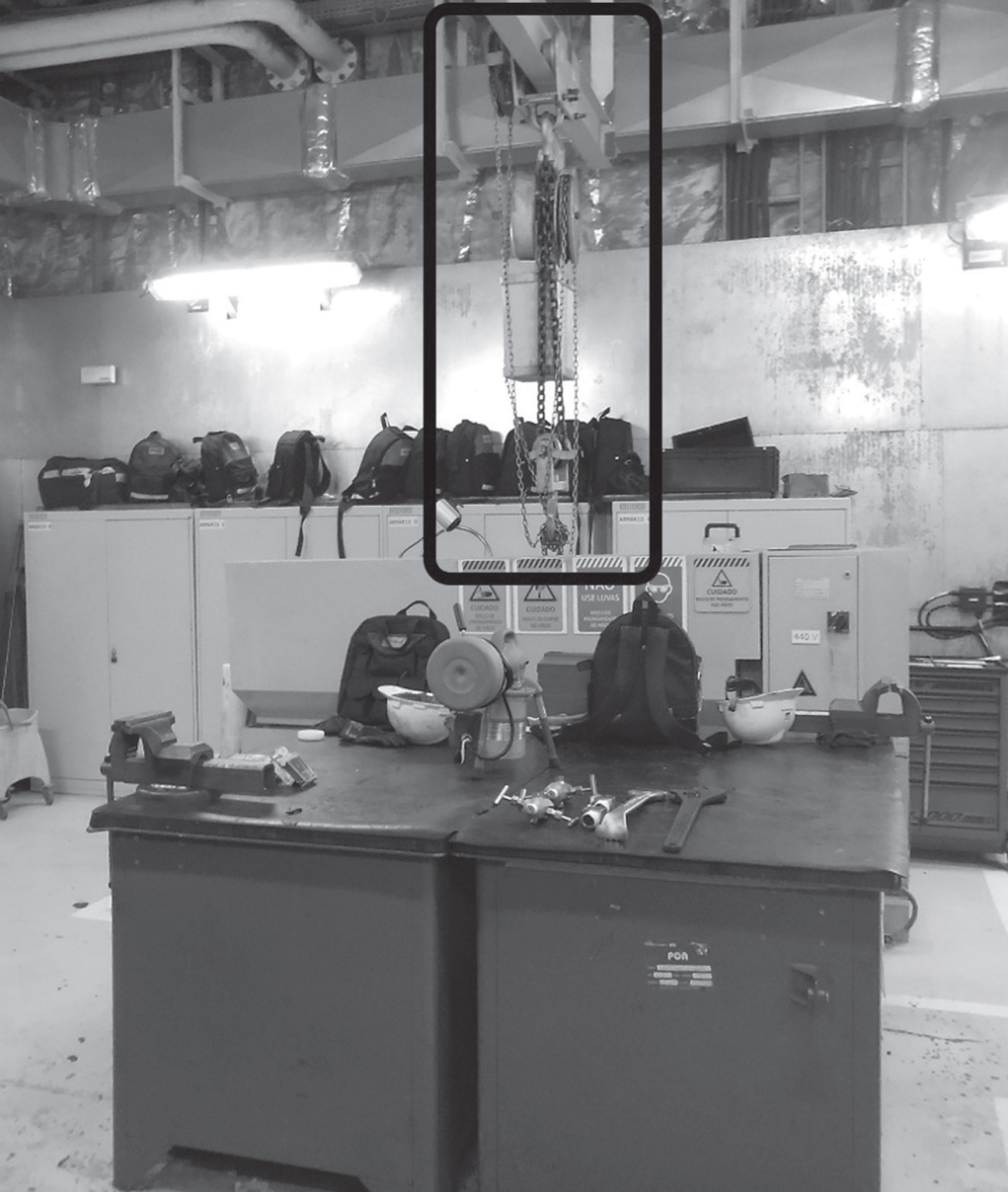
Thus, when moving large equipment, operators found it difficult to lift them high enough to place them on the bench, due to the little space available for this maneuver. Faced with this difficulty, some parts have already had to be maintained on the floor. Furthermore, according to the supervisor, the hoist has a capacity much greater than that needed for the workshop. Therefore, it is necessary to consider both the equipment to be maintained in each workshop, as well as the capacity of the hoist and its distance from the workbench.
In the electrical workshop, it was observed that the monorail was not directed to the test bench, which makes it difficult to move the parts to be maintained.
Another problem observed was the presence of unused equipment, which takes up unnecessary space in the environment, as is the case with the calender machine. Some workers also mentioned that “this (calender machine) comes on every platform and nobody uses it”. This reinforces the need to review the equipment list in future stages of the project, aiming to reduce costs in the project and provide a more adequate and organized space for the performance of the work of these teams.
• Layout and equipment list analysis results
These analyses supported the definition of technical specifications and direct changes in the layout of the workshops, based on discussions with the architecture discipline. Figure 5 shows the preliminary layout of the workshops, as proposed at the beginning of the project, on 05/13/2019. Figure 6 shows the final layout of the workshops in the end of the basic design stage, on 04/15/2020, after the modifications proposed by the ergonomics team.
Fig. 5
Workshop preliminary layout.
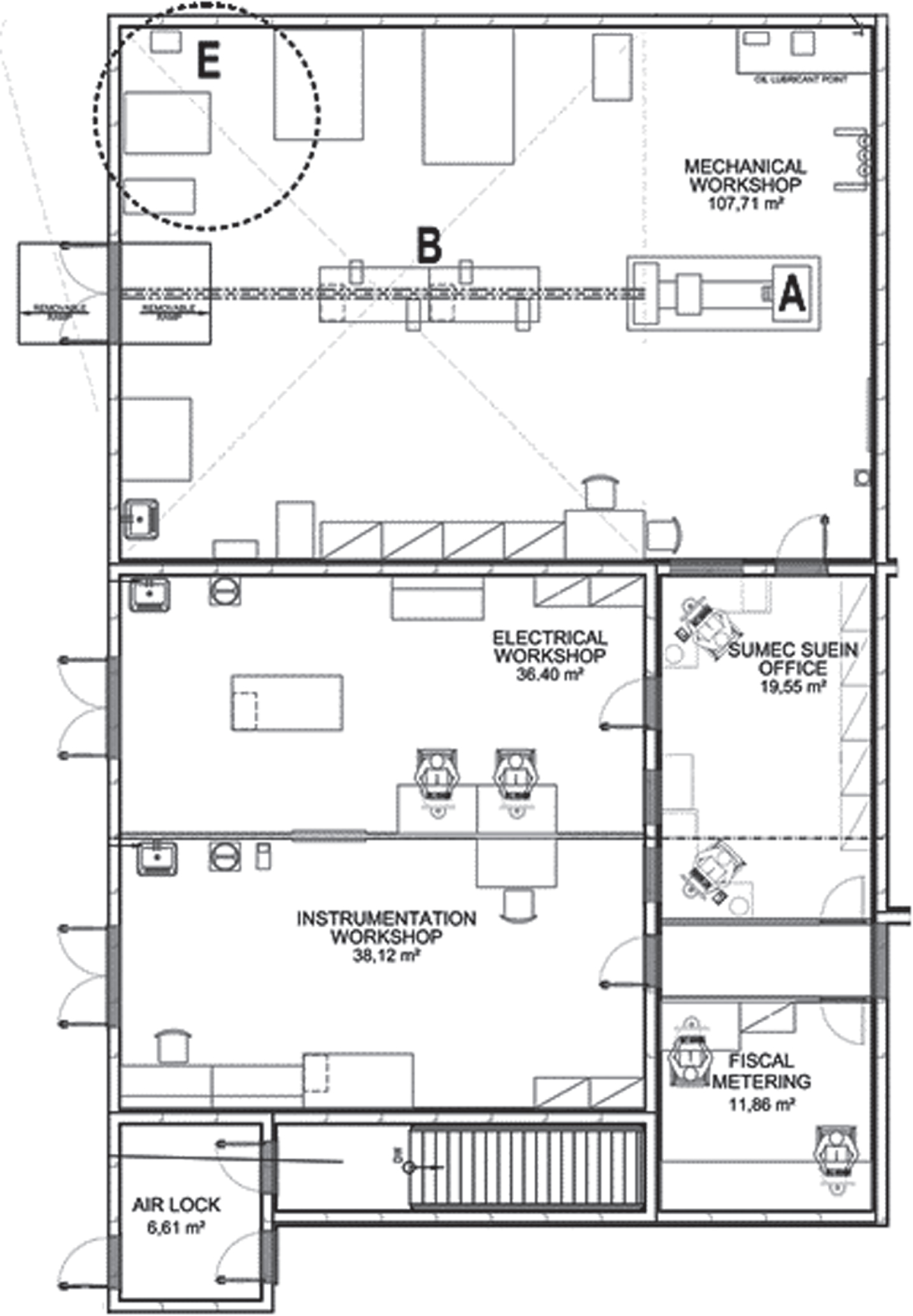
Fig. 6
Workshops’ layout after changes.
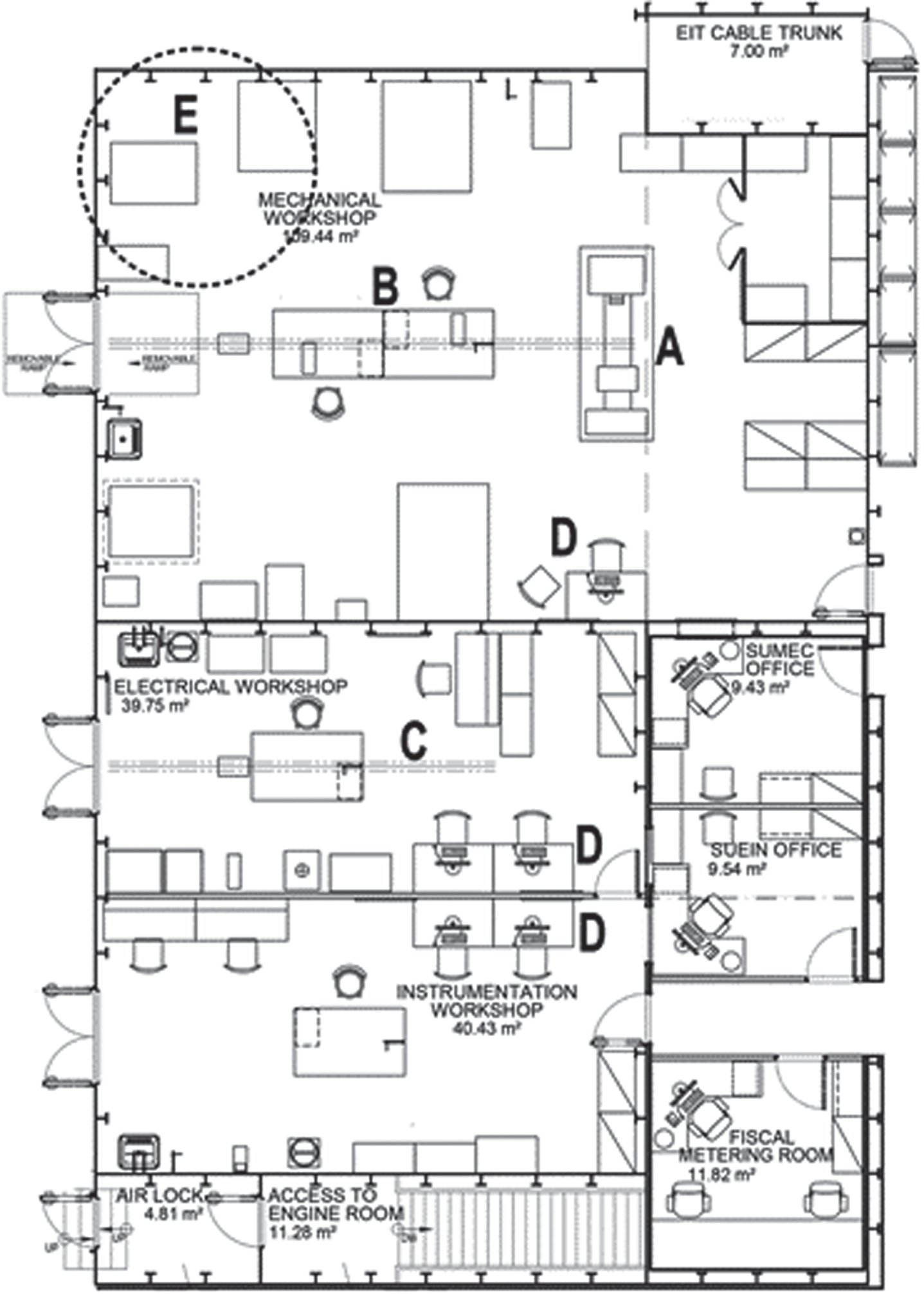
As mentioned above, some modifications identified in the Fig. 6 are:
- Changing position of the lathe (item “A”) in the mechanical workshop, in order to facilitate integration with the monorail;
- In both layouts, the maintenance workbench (item “B”) is located in the center of the shop. In the analysis in reference situations, users confirmed that this would be the most favorable position for working;
- Inclusion of monorail (item “C”) in the electrical workshop for handling equipment of greater weight and/or volume;
- Installation of screens (item “D”) in all workshops to monitor PI parameters;
- The grinding machine equipment was removed, to give adequate space to use the hydraulic press and milling machine equipment (item “E”).
4Discussion
The participation of ergonomics provided reflections on the maintenance work and the contribution of ergonomics and design dynamics. There was the integration of users and designers, by creating discussion forums that encompassed different rationales and stakeholders of the project. This process sought to bridge the gap between real work and the design, based on the reference situations analyses.
This distance was emphasized in the following speech, which is a consensus among reference situations workers: “all design concepts were made to produce, not to operate (...) the person who designed it, seems to me that has no idea what is done here”.
The issue mentioned in such statement can give rise to design inconsistencies that may impact the performance of activities, the integrity of the unit and equipment, the safety of the process and the health of workers [11].
In this project, the ergonomics team’s initial demand was to deliver specifications for the offshore platform areas. However, the knowledge acquired on the work did not only translate into the creation of ergonomics technical specifications. Part of this knowledge was also used to contribute to the technical specifications of other disciplines, in addition to creating layouts and equipment lists.
The chapters addressing technical specifications were previously structured by the project management team, so the specifications’ presentation was divided according to the platforms’ environments, including the workshop. The contributions related to the maintenance crew’s work were inserted mainly in this chapter.
However, the development of this research allowed us to elucidate that the maintenance crew’s work is not restricted to these areas, as maintenance work is done throughout the platform, it also includes administrative and equipment operation activities. Therefore, in addition to the workshops’ specifications, contributions to support maintenance activities beyond the workshops’ area have also been added, such as to provide support points for the maintenance crew in the operational area (Fig. 7). This requirement aims to contribute to reducing displacements to workshops and increase problem-solving efficiency.
Fig. 7
Outcomes for the project.
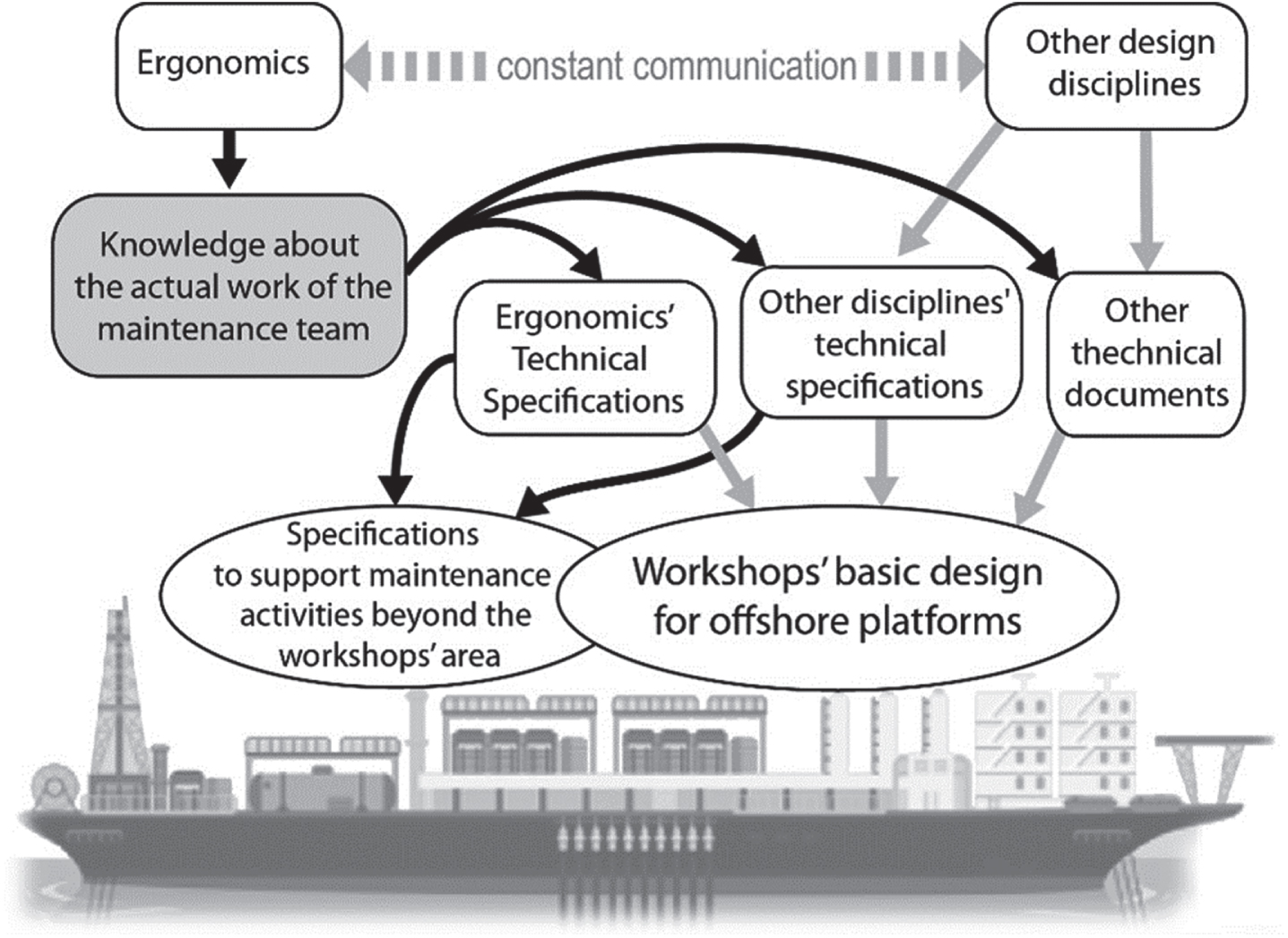
The analysis of the maintenance crew’s work ratified that the knowledge generated goes beyond the technical documents created. It includes new ways of thinking about the project dynamics itself, with greater integration between the disciplines involved. The knowledge about work performed in the reference situations was the basis for requirements presented to designers. It supported the technical decision-making process of the project, which will influence the working conditions on future platforms, its integrity, productivity, reduction of maintenance stoppages and design changes expenses, and reduction of work leave [6, 9].
In the basic design phase, ergonomics’ specifications depend on the possibility of anticipating design decisions. Depending on the level of anticipation, direct specifications can be created, as in the case of the workshop equipment arrangement. In other situations, the specifications depend on future design decisions and are placed as assumptions/constraints to assist designers in the next steps, such as the battery room example.
Thus, ergonomics’ participation does not exhaust the knowledge on the best work practices; instead, it provides elements that increase the margin of maneuver of both the designer of the next phases and the worker of the future units. Coutarel, Daniellou e Dugué [17] state that “the notion of room for maneuver allows us to recover what is offered to the operator, in terms of operating flexibility of operating modes or imposition of constraints, when present during the stages concerning the fabrication of future work facilities”.
These conditions do not replace the need for ergonomists in future stages, alongside design engineers, nor do they disregard the need for spaces for debate and continuous dialogue between the various disciplines. They only provide basic guidelines for the work dimension to be considered in decisions from the early stages of the project, reducing the need for biomechanical efforts, difficulties related to access, the risk of accidents and difficulties in carrying out activities [6, 18–20].
To sum up, the participation of ergonomics during the construction of the new facilities, in the project execution phase, is also relevant so that ergonomics decisions are incorporated into all stages of the project, up to the operation of the offshore units [18–20].
5Conclusion
This work presented the integration of ergonomics in an offshore basic platform design, its collaboration with the maintenance crew’s future work, and its constraints. Ergonomics studies in the basic design stage contributes to costs reduction related to future design changes.
The recognition of the ergonomist as a project stakeholder has not yet been consolidated, however, this study highlighted how the knowledge about work - generated by ergonomics - supports the project.
The ergonomic discipline’s demand is usually directed to contributions related to worker’s health and safety, disregarding their skills to improve the execution of activities and productivity. This disparity was evidenced in the technical specifications construction, where recommendations were not restricted to the workshop environment, extrapolating to other areas of the platform where the maintenance crew also works.
This paper elucidated the possibilities of contribution of ergonomics beyond demands related to health and safety, besides pointing out a cognitive work and an organizational dimension, which is still difficult to be explained and incorporated into design decisions, especially in the basic design stage.
The documents delivered by the ergonomics team reinforced aspects of its development dynamics. As observed in the calender machine example, equipment lists are often replicated from one project to another without updating. Nevertheless, the revision of this document must occur in each new project, both in partnership with other disciplines, and according to the specifics of the future work.
As each design stage involves new decision-making, at different levels, the accumulation of knowledge about the real work - through the role of the ergonomist - must be considered at all these stages [18–20]. Furthermore, it is suggested that both cognitive work and organizational dimension be further researched, to take it into the projects’ context.
The limits imposed on this work, including the availability of places onboard for analysis in reference situations, should be considered. Also, the discussion was restricted to the maintenance crew of the units’ operational department, without considering the work of the outsourced crews and other departments.
Further analysis of offshore maintenance work is required to encompass other crews and see how the design of other areas of the platform impacts the maintenance crew’s work. It is recommended the continuation of ergonomics participation in future project stages, as well as further researches based on this participation. Hence, this work points to the need for new studies on platform maintenance work and the consolidation of ergonomics practice in projects.
Ethical approval
Not applicable.
Informed consent
Not applicable.
Conflict of interest
None to report.
Funding
This study was financed in part by the Coordenação de Aperfeiçoamento de Pessoal de Nível Superior – Brasil (CAPES) – Finance Code 001, and by the Conselho Nacional de Desenvolvimento Científico e Tecnológico (CNPq), both entities linked to the Ministry of Science, Technology and Innovation that foster research in Brazil.
This paper has also benefited from resources provided by CAPES/PRINT 41/2017 public notice, throughout the research project “Management and Innovation for Sustainability”.
References
[1] | Daniellou F . L’ergonomie dans la conduite de projets de conception de systèmes de travail. In: FalzonP, editor. Ergonomie. Paris (FR): Presses Universitaires de France; (2004) , pp. 359–73. |
[2] | Abrahão J , Sznelwar L , Silvino A , Sarmet M , Pinho D , editors. Introdução à ergonomia: Da prática à teoria. São Paulo: Blucher; (2009) . |
[3] | Broberg O . Integrating ergonomics into engineering: Empirical evidence and implications for the ergonomists. Human Factors and Ergonomics in Manufacturing. (2007) ;17: (4):353–66. DOI: 10.1002/hfm.20081 |
[4] | Duarte F . Complementaridade entre ergonomia e engenharia em projetos industriais. In: DuarteF, editor. Ergonomia e Projeto na Indústria de Processo Contínuo. Rio de Janeiro: Lucerna; (2002) , pp. 11–21. |
[5] | Da Conceição C , Broberg O , Duarte F . A six-step model to transform an ergonomic work analysis into design guidelines for engineering projects. Work. (2020) ;66: (3):699–710. DOI: 10.3233/WOR-203212 |
[6] | Duarte F , Lima F . Anticiper L’activité par les configurations d’usage: Proposition méthodologique pour conduite de projet. Activités. (2012) ;9: (2):22–47. DOI: 10.4000/activites.314 |
[7] | Mercado MP , Leite PBC , Marins CP , Tinoco F , Duarte FJCM . The Practice of Ergonomics in the Creation of Technical Specifications for Offshore Platform Projects In: Lecture Notes in Networks and Systems. 1 ed.: Springer International Publishing, (2021) , pp. 217–22. |
[8] | Marins CP , Leite PBC , Mercado MP , Garotti LV , Duarte FJCM . Constructing the Place of Ergonomics as a Design Discipline: The Case of the Basic Design of Oil Platforms. In: Lecture Notes in Networks and Systems. 1 ed.: Springer International Publishing, (2021) , pp. 196–200. |
[9] | Lima F , Duarte F . Integrando a ergonomia ao projeto de engenharia: Especificações ergonômicas e configurações de uso. Gestão & Produção. (2014) ;21: (4):679–90. |
[10] | Conceição C , Silva G , Broberg O , Duarte F . Intermediary objects in the workspace design process: Means of experience transfer in the offshore sector. Work. (2012) ;41: :127–35. DOI: 10.3233/WOR-2012-0146-127 |
[11] | Alonso C , Lima A , Oggioni B , Teixeira M , Oliveira E , Couto M , Duarte F . Contributions of activity ergonomics to the design of an electronic health record to support collaborative mental care of children and youth: Preliminary results. Work. (2020) ;65: (4):187–94. |
[12] | Lipovaya V , Duarte F , Béguin P . The work activity as an interface among different logics: The case of distributing food in a university restaurant. Work. (2018) ;61: (4):647–60. |
[13] | Guérin F , Laville A , Daniellou F , Duraffourg J , Kerguelen A . Compreender o trabalho para transformá-lo: A prática da ergonomia. São Paulo: Edgard Blücher; (2002) , p. 224. |
[14] | Daniellou F . The French-speaking ergonomists’ approach to work activity: Cross-influences of field intervention and conceptual models. Theoretical Issues in Ergonomics Science. (2005) ;6: (5):409–27. DOI: 10.1080/14639220500078252 |
[15] | Jeantet A . Les objets intermédiaires dans la conception. Éléments pour une sociologie des processus de conception. Sociologie Du Travail. (1998) ;40: (3):291–316. DOI: 10.3406/sotra.1998.1333 |
[16] | ABERGO. Brazilian Association of Ergonomics. Norma ERG BR 1002. Código de Deontologia do Ergonomista Certificado [Internet]. 2003 [cited 2021 Dec 13]. Available from: https://www.abergo.org.br/certifica%C3%A7%C3%A3o by selecting PDF link in documents list |
[17] | Coutarel F , Daniellou F , Dugué B . Interroger l’organisation du travail au regard des marges de manœuvre en conception et en fonctionnement. La rotation est-elle une solution aux TMS. Perspectives interdisciplinaires sur le travail et la santé. [Internet] 2003 Dec [cited 2021 Dec 13] 2-5. Available from: https://journals.openedition.org/pistes/3328 DOI: 10.4000/pistes.3328 |
[18] | Duarte F , Cordeiro C . A Etapa de execução da Obra: Um momento de decisões. Revista Produção. (1999) ;9: (22):05–28. DOI: 10.1590/S0103-65131999000400001 |
[19] | Sørensen LB , Broberg O . Integrating ergonomics in design processes: A case study within an engineering consultancy firm. Work. (2012) ;41: :949–55. DOI: 10.3233/WOR-2012-0268-949 |
[20] | Oggioni B , Duarte F , Cordeiro C . Ergonomics in projects of oil platforms in a change context. Work. (2012) ;41: (1):107–13. DOI: 10.3233/WOR-2012-0143-107 |