Preventive action with a population of excavator drivers exposed to whole-body vibration
Abstract
BACKGROUND:
Whole-body vibration is a major cause of lower back pain among employees, and the medical and preventive care teams of occupational health departments are often confronted with lower back pain problems among machine operators.
OBJECTIVES:
The objectives of this research are to determine the number of excavator drivers exposed to whole-body vibration levels above 0.5m/s2, identify other exposure factors that may contribute to back pain, and propose corrective measures.
METHODS:
Vibration measurements were carried out on individual excavator drivers while they were observed carrying out working tasks, after which prevention advice is given. Factors which determine vibration levels are logged on to a database.
RESULTS:
The multivariate analysis of several determining factors shows vibration exposure levels vary depending on the varied work tasks being carried out.
CONCLUSION:
This study identifies exposed employees among excavator operators. For each workstation, the determining factors that could explain the high exposures to vibrations are identified. This work shows the important role of tasks on exposure levels. A better adaptation of the tools used to carry out work tasks would allow a decrease in the vibration level of this type of machine.
1Introduction
This paper reports the findings of a study on exposure to whole-body vibration in excavator-driving employees population between December 2013 and December 2016. This action was part of a Multi-Year Contract of Objectives and Means (CPOM) in partnership with DIRECCTE (Direction Régionale des Entreprises, de la Concurrence, de la Consommation, du Travail et de l’Emploi) and CARSAT (Caisse d’Assurance Retraite et de la Santé au Travail).
Whole-body vibration (WBV) is considered to be important occupational risk factor contributing to the development of lumbar pathologies and pain that have a major socio-professional impact for the workers and their families [1, 2]. For example, exposure to WBV in construction workers increases the risk of hospitalization for lumbar disc herniation problems [3]. A systematic literature review [4] and meta-analysis shows that workers who are exposed to WBV have an increased risk of both low back pain and sciatica compared to non-exposed groups. The pooled estimates of the risk are approximately doubled. The influence of tasks on vibration levels has been described in several studies. Vibration levels have been studied in agricultural equipment operators exposed to tremors and shocks. These exposure values depend on the tra-ctors used and the tasks performed, such as mowing, raking, tilling, road travel, etc. [5]. A study on heavy equipment operators of a front-end loader shows the role of task exposure and tire configuration [6]. This study found significant differences in exposures between work tasks. The scooping and dumping task have the highest exposures. In the current study, vib-ration levels on excavator operators are studied for different tasks.
Data from the Occupational Health Service’s medical of Ales and Lozere, CMIST, (Interprofessional Medical Centre for Occupational Health in the north of the Gard in France), shows a particularly high rate of lumbar pathologies in the machine operator pop-ulation. Among machine operators 23.5% of employees suffer from pathologies such as low back pain, sciatica or disc herniation. Statistics from CARSAT’s prevention services show figures that these rates of injury are well above the national average in terms of absences and disabilities due to accidents at work and other occupational diseases (Table 1). During workplace visits, occupational physicians and a multidisciplinary team of the occupational health service providers are able to identify situations where these employees were at risk of exposure to vibration ma-king it possible to classify excavator drivers as emp-loyees exposed or not exposed to vibration, but they lacked precise exposure values [7]. There is reliable measuring equipment available to quantify exposure to WBV. By quantifying the exposure, prevention measures can be used to reduce exposure levels. All the methodology is well described in ISO/TR 25398 [8] which provides guidelines for the assessment of WBV exposures for operators of earth-moving mac-hinery. This standard specifies the determining factors of vibrations and states that the vibration levels are specific to the workstation and the work situation being studied. The following determining factors are mentioned: the level of maintenance of the machine, the type of driving, the behavior of the driver, and the condition of the soil. The standard provides guidelines for vibration measurements, the calculation of the A (8) value, and specifies that these exposures are only representative for the type of tasks performed by the machine. All these elements have prompted us to take action on whole-body vibration exposure in this population.
Table 1
CPOM vibrations - CMIST Alès - DIRECCTE Languedoc Roussillon - Carsat Languedoc Roussillon: Statistics on work accidents and occupational diseases North of Gard and Lozere
Statistical data 15/12/2014 | |||||
For 1000 salariés | France - Moy 2008 á 2012 | Secteur CMIST Alès -Moyenne 2009 á 2013 (5 ans) | |||
B04 TP national | Engins | % | Caristes | % | |
ATAA1 | 58 | 78 | 135% | 42 | 73% |
ATIP2 | 5.1 | 6.8 | 133% | 3.7 | 73% |
IJAT3 | 3,796 | 4,057 | 107% | 2,981 | 79% |
MPAA4 | 3.8 | 3.2 | 84% | 6.0 | 158% |
MPIP5 | 2.1 | 3.6 | 176% | 4.6 | 221% |
IJMP6 | 767 | 1,072 | 140% | 1,638 | 214% |
ATMP AA7 | 62 | 81 | 132% | 48 | 79% |
ATMP IP8 | 7.2 | 10.5 | 146% | 8.3 | 115% |
IJ ATMP9 | 4,563 | 5,129 | 112% | 4,619 | 101% |
5-year mean | 243,996 | 1,318 | 5,571 | ||
Carsat LR - established | |||||
synthesis le 30/03/2015 |
1ATAA: work-related accident with work interruption, 2ATIP: work accident with permanent incapacity. 3IJAT: daily indemnity due to an work accident, 4MPAA: occupational disease with work interruption. 5MPIP: occupational disease with permanent incapacity, 6IJMP: daily indemnity due to an occupational disease. 7ATMP AA: work related accident and occupational disease with work interuption. 8ATMP IP: work related accident and occupational disease with permanent incapacity. 9IJ ATMP: daily indemnity due to an work accident and occupational disease.
The objectives of this study are to identify subjects exposed to vibration with A (8) values >0.5m/s2, i.e. the Exposure Action Value (EAV), or above the Exposure Limit Value (ELV) of 1.15m/s2, in order to specify the classification of exposed and unexposed employees.
According to Directive 2002/44/EC transposed into French law by Decree 2005–746 (04 July 2005) on vibrations transmitted to the whole-body, the daily value triggering the prevention action is fixed at a threshold of 0.5m/s2, above which the employers must establish a risk management program with a daily exposure limit threshold of 1.15m/s2 not to be exceeded.
The medical teams of the occupational health ser-vices are responsible for collecting information in the occupational health file on the exposures of mon-itored employees and the traceability of exposures (Article L4624–8 of the Labour Code; Law no. 2016–1088 of 8 August 2016). It is also important to have a more accurate estimate of the whole-body vibration risk for employees in the geographical area of Alès and Lozere (north of the Gard and Lozere, France), to be able to compare it with the national results of the INRS database [10]. In this study, two populations were examined in detail due to a suffi-cient number of subjects: forklift drivers and excavator drivers, the results of which are described in this article.
2Methodology
2.1Study population and selected sample
The study focuses on the exposure of employees in the North of Gard and Lozere to vibration, monitored by the CMIST Gard Lozère occupational health service and supervised by a prevention contract signed with the DIRECCTE and CARSAT. This contract sets quantitative and qualitative objectives for the actions carried out by the occupational health service on the population of machine operators for a period of 4 years between 2013 and 2016. Machine operators were regularly monitored and information is recorded on these employees in the occupational health file. Exposure is assessed a priori in three classes (minimal, medium, high) based on the knowledge acquired by the health professional at the workplace and the company during their visit to the workplace site. Workers with minimal exposures are assessed a priori below 0.5m/s2. Workers with high exposures are considered above 1,15m/s2. The medium class is the class of the workers between these two values.
Data from occupational health records are extracted into a database and evaluated using the business object database management software [11]. In total, the occupational health service supervises 643 machine operators in 220 companies (truck drivers, loaders, shovels, various forestry equipment, tractors etc.).
This study focused on responses of operators of machines driving more than 4 hours a day. At the beginning of the study, an initial telephone contact by IPRP (occupational risk prevention worker) clarifies the type of workstations and the number of workstations concerned. The IPRP is a pre-ventive agent with technical or organisational competence, whose mission is to prevent occupational risks and improve working conditions. He intervenes in workplace actions of diagnosis and advice, support and follow-up. The IPRP’s field of action is in disciplines such as ergonomics, toxicology, industrial hygiene, and/or work organization. A standard report is produced for each workstation giving the employee’s age, driving experience, types of tasks performed, working hours, workplace characteristics and routes taken by the machine operator. He asks the employee about his actual driving time. Depending on the company, IPRP also questions the employer or manager for an assessment of the actual driving time. This assessment is essential since it influences the value of the employee’s exposure to vibration over the working day. All the characteristics of the machine are noted; state of the seat, tires, number of hours of use recorded, brand as well as the type of soil.
2.2Vibration measurement methodology
Acceleration measurements at the points where vibrations enter in the human body were carried out in accordance with the requirements of ISO 2631–1:1997 [7]. Measurements were made using a vib-rometer equipped with a triaxial accelerometer inserted in a cup [9] on which the employee sits, making it possible to assess accelerations on the seat along 3 orthogonal axes: X (front-rear), Y (left-right) and Z (top-down), and a mono-axial accelerometer placed on the floor (EvecFloor), as close as possible to the central axis of the seat, allowing the acceleration to be measured along the vertical axis Z. This exposimeter (vib@work seat) is in the form of a standard semi-rigid disc, positioned on the seat of the machine seat. It consists of a triaxial accelerometer, an electronic circuit for weighting and storing signals and an operator presence detection system (Fig .1). A wireless transmission system allows the data to be exported to calculation software that can be installed on a laptop computer or handheld organizer. The measurement of floor vibrations is measured using a three-axis exposure meter (vib@work floor). Coupled with the vib@work seat, it allows the determination of the efficiency factors of seats (also called S.E.A.T. factors), public works machinery.
Fig. 1
Installation of vibration measuring devices on the seat and floor of the cabin.
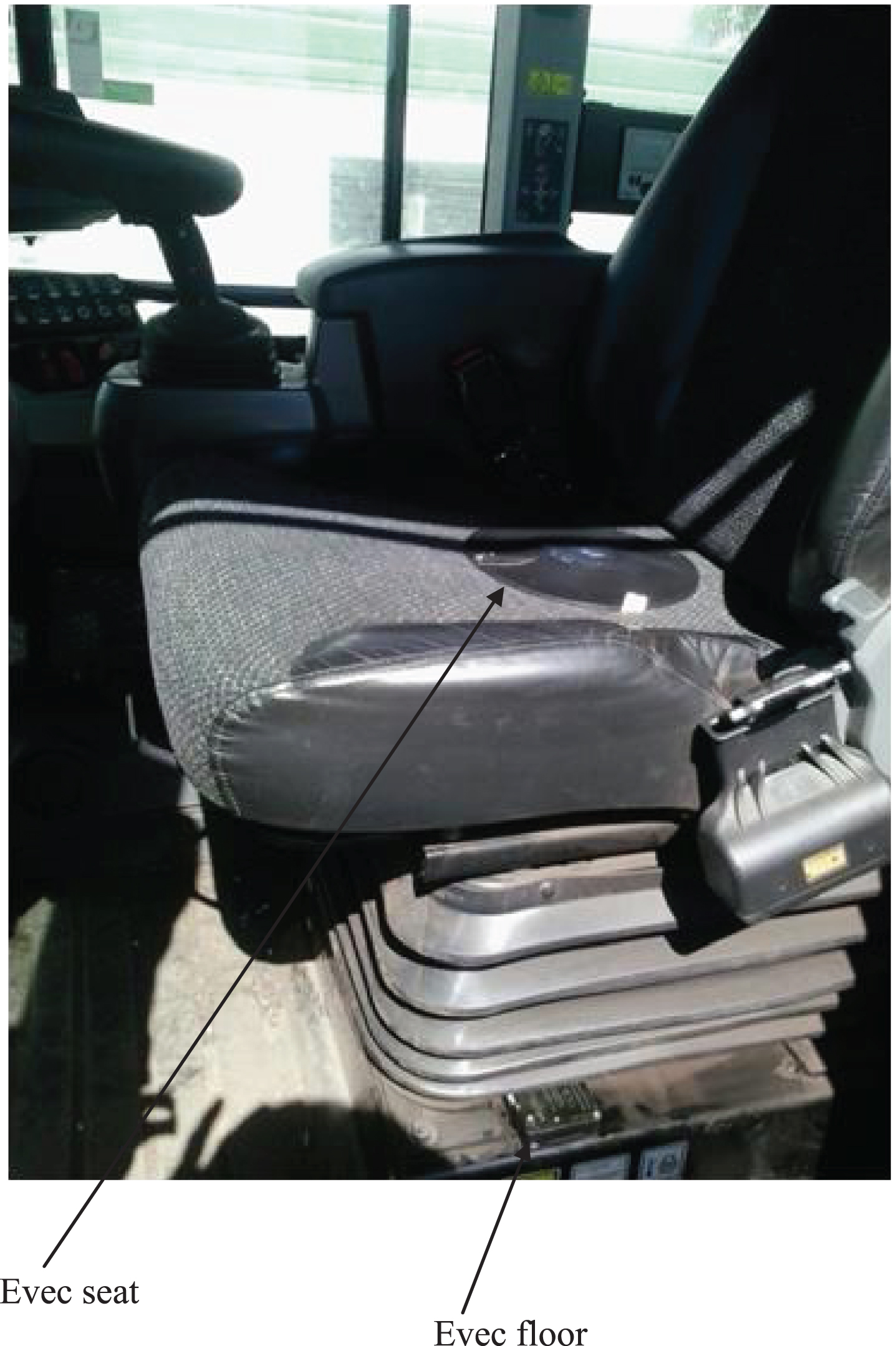
This type of equipment (Fig .1) makes it possible to evaluate two parameters simultaneously, on the one hand the equivalent acceleration (Aeq in m/s2) to which the driver is subjected and on the other hand, the SEAT factor, a ratio characterizing the tra-nsmissibility of the seat along the vertical Z axis. The SEAT factor is the ratio between the acceleration measured at the seat in the vertical axis and the acceleration measured at the machine floor (awzs (seat)/awzf (floor)) The EvecFloor therefore makes it possible to evaluate the efficiency of the seat by calculating the ratio of seat vibration to chassis vibration. If the value is>100%, the seat transmits vibrations and even amplifies them and if the value is<100%, it reduces vibrations. For reference, it is considered that a quality seat must have a SEAT factor of less than 80% for this type of equipment [10].
Once the measurement sensors are installed, the machine operator resumes his work, and the IPRP is in the observation phase. He observes the employee in his work tasks, which allows him to specify certain particularities of the work of the machine operator that may have an influence on the level of exposure. Observation times vary from 20 minutes to 4 hours [12]. The sensors are then retrieved and the results are transferred to the computer for analysis with the EvecSensorDuo capture software and the EvecViewerDuo analysis software. The results are calculated by taking into account three measurement periods: total measurement period (TPM) which includes all phases of the employee’s work including phases where the employee is not exposed but the sensor remains in place, actual exposure period of actual recording of vibrations transmitted to employees measured by the sensors (PE), and finally actual driving period (PU). The seat efficiency factor is also calculated.
2.3Data analysis
Following each IPRP intervention, an Excel 2007 database containing data concerning the company, the employee, the characteristics of the equipment, the condition of the equipment (obsolescence, seat, tires), the results, the employee’s activity data (tasks performed) and the type of soil is filled out.
In addition, a multiple logistic regression analysis type ANCOVA was performed with XLSTAT software. A covariance analysis is conducted, using the Fisher test, that calculates the type I SS (sum of type I squares) and III SS errors (sum of type III squares) and estimated exposure values for the various explanatory factors. The dependent variable studied is A(8).
The qualitative explicative variables are:
– Tasks with 5 modalities: excavation on soft ground, excavation on pavement, compacting, excavation on rock and pebbles, Hydraulic Rock Breaker (BRH) [Fig .2].
– The soil has two modalities: bad state (stoned soil, rough soil, soil with holes) or good state (uniform soil, work on asphalted road).
– The type of excavators with two modes: crawler excavators or wheeled excavators.
– The qualitative explanatory variables chosen are the level of experience in years, and the age of the equipment in years from the date of the study.
Fig. 2
Wheel excavator operator working with a rock breaker for foundations preparation.
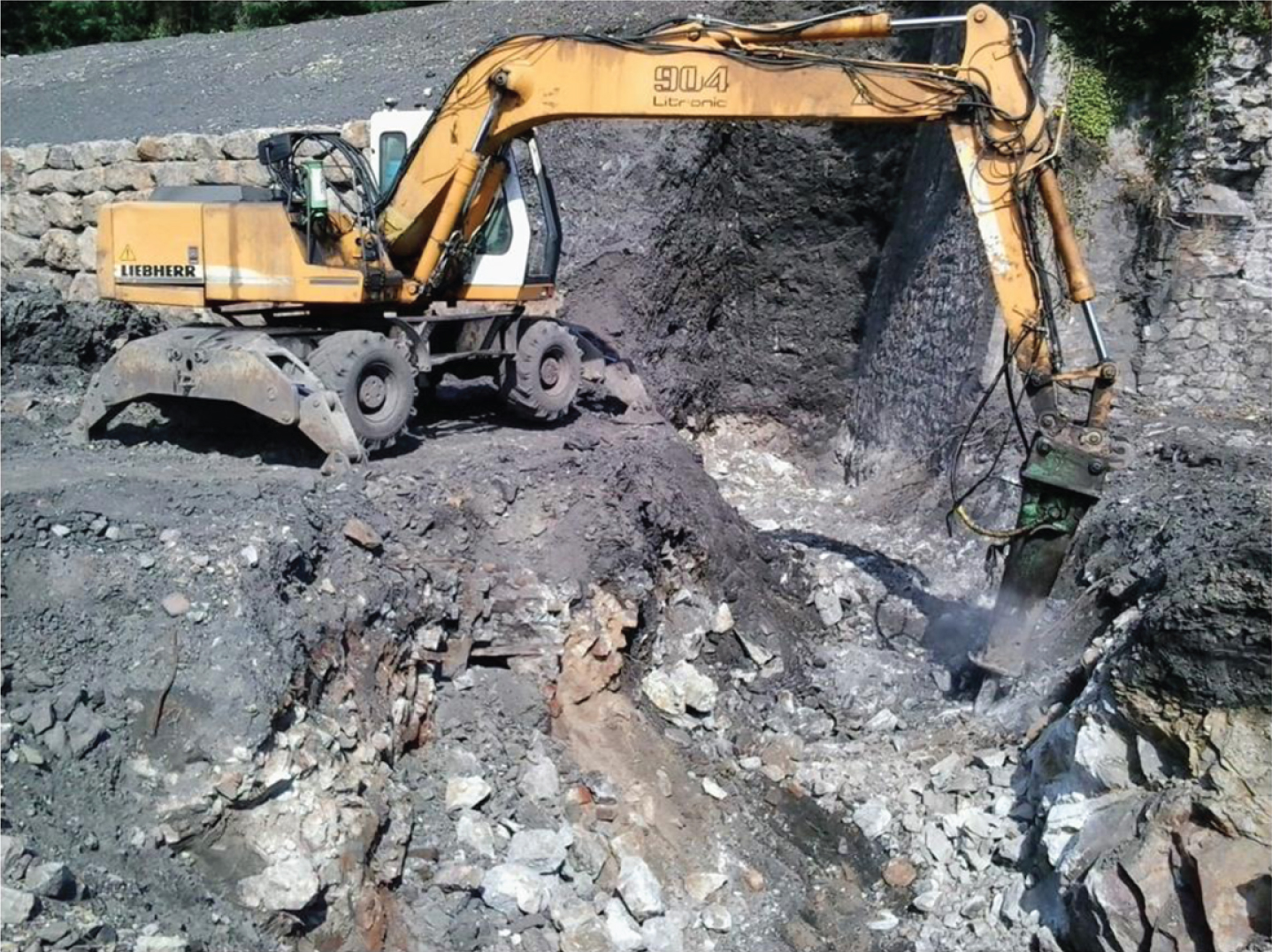
3Results
3.1General data and specific work requirements
Fourty-three measurements were performed in excavator drivers whose median age was 35 years ranging from 31 years (25th percentile) to 45 years (75th percentile) (Table 2). The drivers worked in 14 companies with sizes ranging from 3 to 120 employees. They carry out public works sites, or for private individuals. They dig trenches on roadways, on hard or soft ground (excavations), They can use BRH. The effective working time on a shovel is between 6 and 8 hours. Only 5 drivers drive between 3,30 and 5 hours. They drive very little with their machines. The machines are wheeled excavators (Fig .3) or crawler excavators (Fig .4).
Table 2
Descriptive statistics on the age of drivers
Statistique | Age |
Number of observations | 42 |
Minimum | 19.000 |
Maximum | 54.000 |
1st quartile | 31.250 |
Median | 35.500 |
3rd quartile | 45.500 |
Average | 38.119 |
Variance (n-1) | 86.546 |
Standard deviation (n-1) | 9.303 |
Fig. 3
Worker driving a pneumatic shovel and digging a trench on a road.
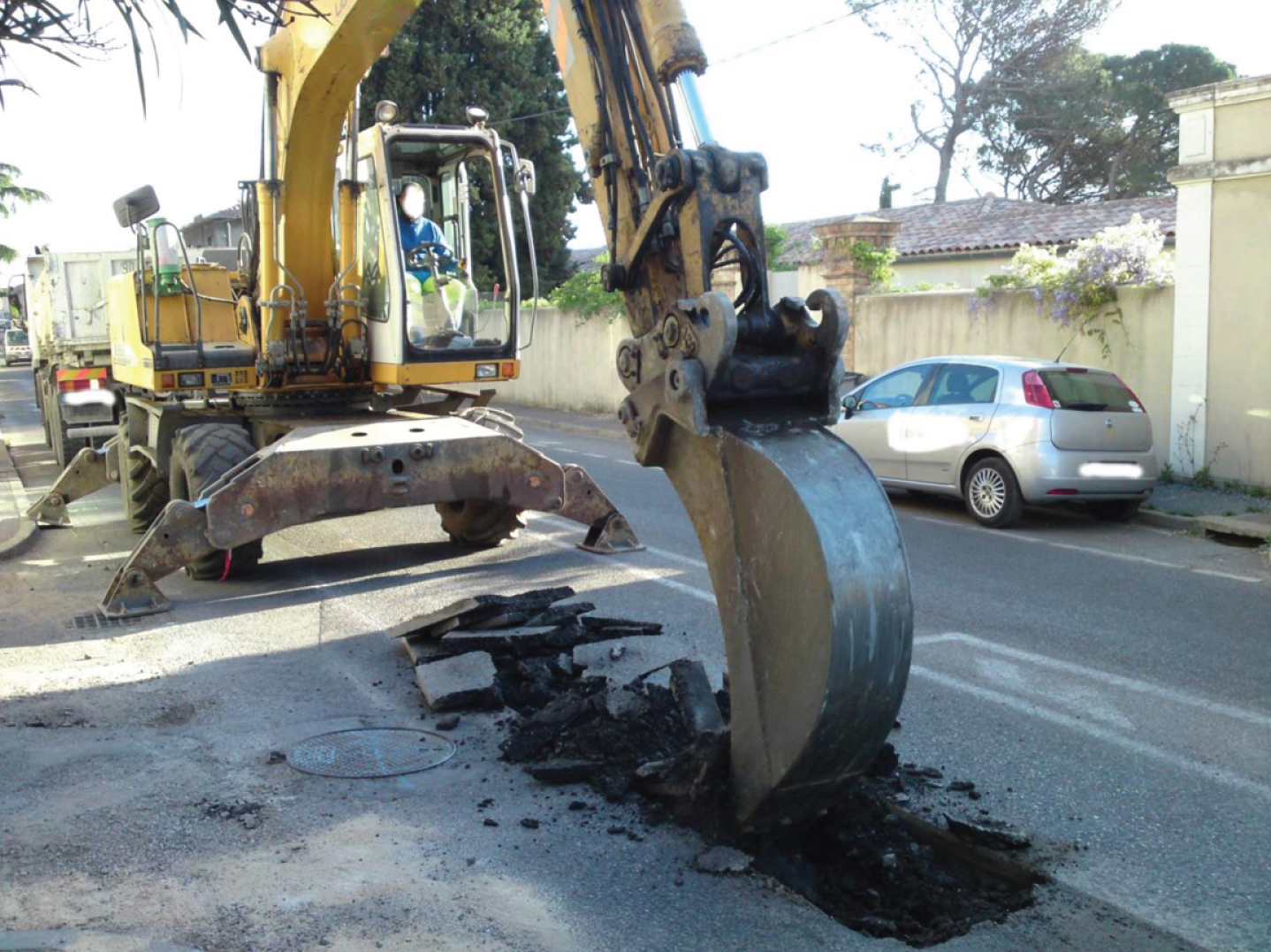
Fig. 4
Worker driving a crawler excavator on a quarry road.
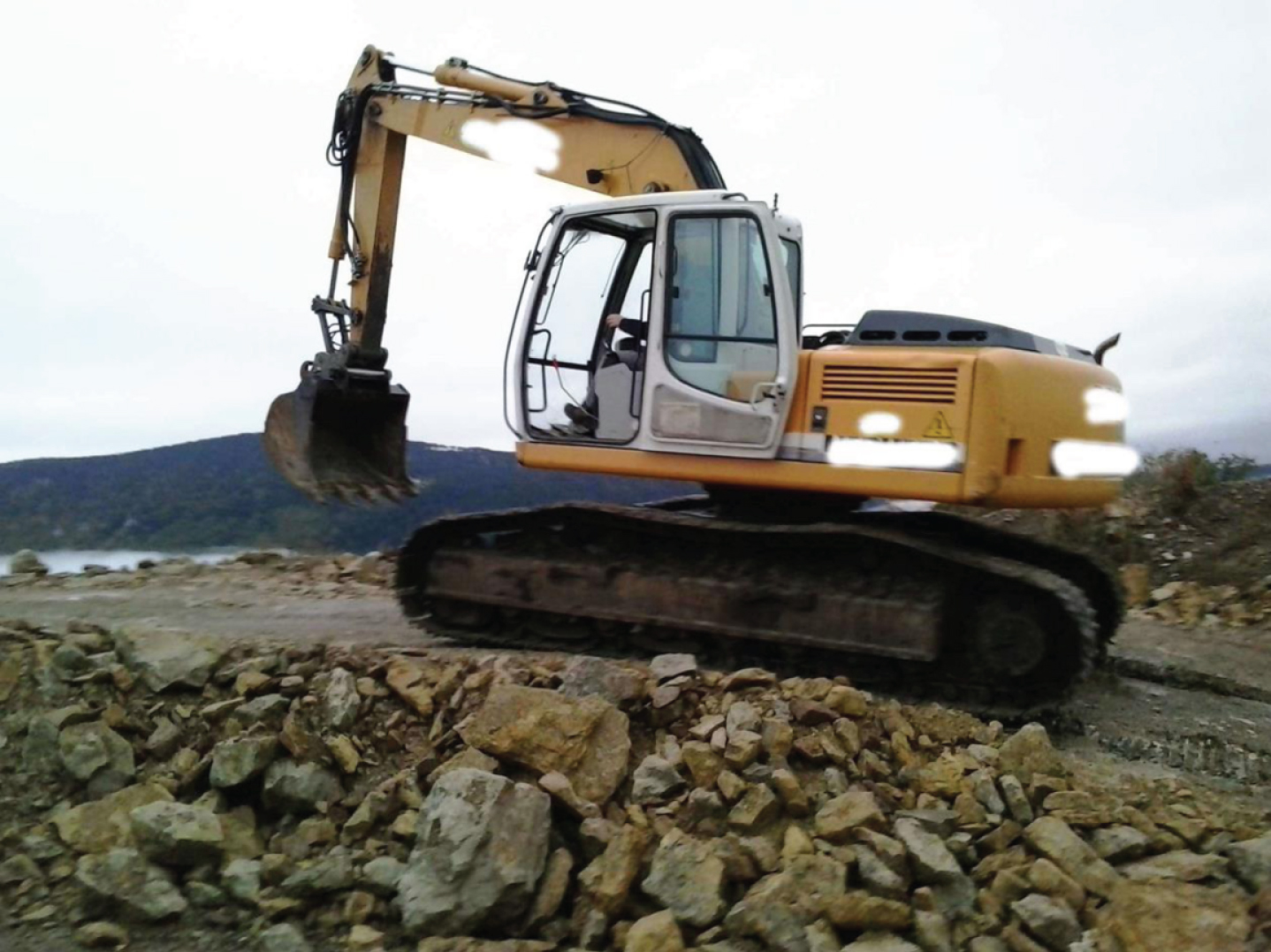
3.2Specific data
For the 43 measurements, we calculated an average of the values A (8) (equivalent continuous acceleration over 8 hours) at 0.548m/s2. The median is 0.560m/s2. The dispersion of the values ranges from 0.355m/s2 (25th percentile) to 0.695m/s2 (75th percentile).
The dominant X-axis is the dominant axis (front-rear vibrations) for 41 measurements. There are A(8) values quoted on the dominant Z axis for 4 measurements. Of these 4 measurements 3 are below 0.4m/s2 and one measurement is at 0.69m/s2.
Seat efficiency factors (SEATs) are rated between 48 and 80% for 28 measurements and for 16 measurements the seats have a SEAT between 84 and 108%.
An ANCOVA multiple linear regression analysis for the selected model was performed. For this ANCOVA analysis, the application conditions are satisfied: the different exposure measurements are independent, there are no more explanatory variables than exposure measurements, the residues are independent and are distributed normally. The following correlation is found: coefficient R2 at 0.448 and an adjusted R2 0.338 (Table 3).
Table 3
Regression of variable A8
Adjustment coefficients (A8) | |
Observations | 43.000 |
Sum of the weights | 43.000 |
DDL | 35.000 |
R2 | 0.448 |
R2 adjusted | 0.338 |
The covariance analysis using the Fisher test shows a significant result (p=0.002) (Table 4). The ISS (sum of type I squares) and IIISS (sum of type III squares) type analyses allow us to know the impact of the explanatory factors and their significance (Table 5). Both analyses are significant for the task factor (p=0.001). The analysis is not significant for the factors of age of the equipment, driving experience, and type of equipment. The table of standardized beta coefficients (Table 6) is significant for soft field excavation and pavement excavation tasks.
Table 4
Analysis of variance (A8)
Source | DDL | Sum of squares | Mean of squares | F | Pr>F |
Model | 7 | 0.726 | 0.104 | 4.062 | 0.002 |
Error | 35 | 0.894 | 0.026 | ||
Total corrected | 42 | 1.620 |
Calculated against the model Y=Mean (Y)
Table 5
Analysis type I sum of squares (A8)
Source | DDL | Sum of squares | Mean of squares | F | Pr>F |
Driving experience | 1 | 0.044 | 0.044 | 1.736 | 0.196 |
Age of the equipment | 1 | 0.019 | 0.019 | 0.756 | 0.391 |
Tasks | 4 | 0.657 | 0.164 | 6.431 | 0.001 |
Shovel | 1 | 0.006 | 0.006 | 0.216 | 0.645 |
Analysis type III sum of squares (A8) | |||||
Driving experience | 1 | 0.003 | 0.003 | 0.125 | 0.726 |
Age of the equipement | 1 | 0.026 | 0.026 | 1.035 | 0.316 |
Tasks | 4 | 0.639 | 0.160 | 6.256 | 0.001 |
Shovel | 1 | 0.006 | 0.006 | 0.216 | 0.645 |
Table 6
Standardized coefficients (A8)
Source | Value | Standard error | t | Pr> |t| | Lower limit (95%) | Upper limit (95%) |
Driving experience | –0.046 | 0.130 | –0.353 | 0.726 | –0.310 | 0.218 |
Age of the equipment | –0.140 | 0.137 | –1.017 | 0.316 | –0.418 | 0.139 |
Soft excavation | –0.601 | 0.187 | –3.214 | 0.003 | –0.981 | –0.222 |
Roadway excavation | –0.517 | 0.196 | –2.643 | 0.012 | –0.914 | –0.120 |
Packing | 0.080 | 0.177 | 0.449 | 0.656 | –0.281 | 0.440 |
Rock and stone excavation | –0.036 | 0.185 | –0.194 | 0.847 | –0.411 | 0.339 |
Hydraulic rock breaker | 0.000 | 0.000 | ||||
Crawler excavators | 0.070 | 0.150 | 0.465 | 0.645 | –0.235 | 0.374 |
Tire excavators | 0.000 | 0.000 |
The predictions made with the model show estimated exposure averages of 0.365 for excavations on soft ground, 0.447 for excavations on pavement, 0.646 for work on stones and rocks, 0.665 for work with BRH, 0.703 for settlement with the back of the bucket.
4Discussion
This study dealt with vibration levels in population of excavator drivers. For the subgroup of wheeled excavators drivers, the median values are 0.590m/s2 between 0.390m/s2 (25th percentile) and 0.720m/s2 (75th percentile). For crawler excavator operators, the median is 0.535m/s2 between 0.343m/s2 (25th percentile) and 0.688m/s2 (75th percentile).
The INRS results [10] find a median of 0.65m/s2 for wheeled excavators between 0.50m/s2 (25th percentile) and 0.8m/s2 (75th percentile). For crawled excavators, they find a median at 0.5m/s2 between 0.4m/s2 (25th percentile) and 0.6m/s2 (75th percentile). These results are therefore comparable to those found by the INRS.
The time of exposure to vibrations determines the daily value A(8). For the 43 drivers, 37 drive between 6 and 8 hours and 6 employees drive between 3,30 hours and 5 hours. The median exposure value for these 6 employees is 0.320m/s2. These values therefore reduce the median values found in the complete groups.
The dominant axis that determines the value A(8) is found in the forward and reverse direction (X axis) for 39 measurements. This result is explained by the nature of the tasks, which are excavation with forward and backward movements of the excavator arm.
The tasks performed are, according to the ANCOVA analysis, the factors that most influence the level of exposure. Excavation tasks on soft ground and excavation tasks on pavements give the lowest levels of exposure. This makes sense for working on soft soil, which results in less force deployed by the excavator arm and therefore less transmitted vibration. For roadside excavation work, the work was done under good excavation conditions: excavator arm in the axis of the excavator, no work at the end of the boom, small bucket adapted to roadside work, excavator in static position [Fig .3]. Working with BRH exposes more to vibration due to the impact of the BRH tool on the material [13, 14].
The compression work (soil compacting work with the bucket) is the most exposed. The bucket of the excavator is not a suitable tool for the compacting task. Similar results highlight the significant role of tasks and high levels of exposure when working on rock [14, 15].
The level of exposure to whole-body vibration was measured by considering the strongest measurement in one of the three axes and reported over 8 hours. This method gives an average value of the amount of vibratory energy. It is a good reflection of exposure to continuous or intermittent mechanical vibrations. In this sample of excavator drivers, the tasks do not lead to peaks of exposure that can be generated by rolling machines on poor ground causing shaking [5]. The measurement method chosen in our study therefore seems to be a good reflection of the level of exposure to vibration.
In this study, the actual driving time of employees is evaluated by interviewing the employee. This time estimate was, in the majority of cases, also validated by the employer. This estimate is major because it will condition the value of A (8). For a more accurate estimate, direct observation of the different work phases and exposure phases should be used. vibration exposures have been evaluated by comparing the values following the employee’s self-reporting, the employee’s interview by the preventive agent, and the direct observation of exposure times by the preventive agent [16]. They concluded that the employee’s self-reporting method is unreliable, especially if the work and tasks are highly variable. They propose methods by interviewing the employee or by direct observation for the estimation of exposure time, the best method remaining the direct observation of exposure periods. The role of the seat is effective in attenuating vibrations in the Z-axis (top-down). This predominant level of vibration in the Z axis is found for machines that run a lot like forklifts [17].
A systematic literature review [18] insists on the determining factors classified in the behaviour and attitude group that increase the level of vibration: better seat efficiency is noted among forklift drivers who weighed less than for those who were heavier. The driver’s posture when driving influenced the amplitude of vibration. The authors also find studies showing the role of the speed, driving experience and ground type on the vibration magnitude. The authors conclude that the two factors that have the most influence on the vibration level are driving speed and seat suspension type. For the type of equipment studied in this research, the role of the seat in vibration attenuation is less important. Indeed, vibrations for excavator conductors are predominant for the X axis. The seat therefore has little action in reducing vibrations for excavator operators.
A recent study [19] also goes in this direction. They evaluated seat vibration attenuation in the X, Y and Z axes for scraper, bulldozer and truck drivers in the mining sector. They concluded that seats with air or mechanical suspensions are effective in the Z axis but not in the X (front-rear) or Y (lateral) axes. Even if the seats do not have any effect on vibrations in the X-axes and Y-axes, it is still essential, to fit the excavators with good quality seats with lumbar support and 3- or 4-point belts, because these seats play an important role in maintaining less constraining postures [10].
The driving speed of the machines is recognized as an important factor in aggravating vibrations [18]. For the tasks performed by the excavator drivers in this study, the work is static, so speed has a minor role on the vibration level. It is chosen the employee’s level of experience as the determining factors for exposure levels [18], assuming that an employee with more driving experience could have better control over the handling of the excavator. It is selected the age of the machine as an aggravating factor, assuming that it was a factor that aggravated exposure levels. These two factors had been found in studies as explanatory factors [15].
The type of equipment is well known as a determining factor because exposure levels are normally higher for wheeled excavators than for crawler excavators [10]. Tracked excavators are stable machines that move little and have high performance for excavation tasks. Wheel excavators are more mobile, can operate on any type of soil but are less efficient for excavation tasks. They sometimes work to the maximum of their performance. All these elements explain the higher level of vibration generated by working with wheel excavators compared to crawler excavators.
This study did not highlight the role of these explanatory variables with the ANCOVA analysis on our model. This can be explained by the small number of measurements made and the lack of power of the study. The two other essential factors responsible for low back pain, namely constraining postures and heavy loads are not studied in this work [20, 21]. Moreover, in this study, even if driving excavators remains the main task, drivers are also versatile and also perform maneuver tasks in support of their colleagues with very constraining handling and postures. Finally, an important factor not evaluated in this study is the effect of education on good driving and working practices for machine operators.
An experimental study was conducted [22] on 6 backhoe loader operators by comparing vibration levels before and after education. They found that providing of the short education is an average reduction in the whole-body vibration exposure of 22.5%.
As part of the medical follow-up and workplace actions carried out by CMIST Ales Lozere professionals, many actions and prevention advice specific to machine operators are carried out, but whose effect has not been evaluated. This type of experimental action is a good idea for evaluation.
5Conclusion
This study makes it possible to determine which machine operators selected in the occupational health files are exposed to deleterious vibration levels. For each job study, it is possible to identify the factors determining high vibration levels and then propose prevention measures to employees and companies.
This work shows the important role of tasks on this type of exposure. The exposure level for excavator drivers is predominant in the X axis. The seats have little effect on vibration damping in this axis. The correct choice of an appropriate tool for a type of task must allow a reduction in the level of exposure.
For each category of driven vehicles and tasks performed by the operators of vehicles there is a specific model, with different determining factors explaining the levels of vibrations generated.
Based on this precise knowledge, concerning the explanatory factors and tasks, the prevention messages and education provided by health professionals to machine operators, will be more adapted and oriented in a more specific way. Research work in col-laboration with manufacturers, in particular on damping devices on excavator arms, should be conducted to reduce vibration levels on this type of machine.
Conflict of interest
The authors state that they have no conflict of interest.
Acknowledgments
The authors thank Mr. Cabanat and Mrs. Garcia (CMIST), Mr.. Velut (CARSAT) and Mr. Mampouya (DIRECCTE) for their support in the realization of this work.
References
[1] | Bovenzi M , Rui F , Negro C , D’Agostin F , Angotzi G , Bianchi S , Bramanti L , Festa G , Gatti S , Pinto I , Rondina L . An epidemiological study of low back pain in professional drivers. Journal of Sound and Vibration. (2006) ;298: (3):514–39. |
[2] | Johanning E . Whole-body vibration-related health disorders in occupational medicine–an international comparison. Ergonomics. (2015) ;58: (7):1239–52. Whole-body vibration. |
[3] | Wahlström J , Burström L , Johnson PW , Nilsson T , Järvholm B . Exposure to whole-body vibration and hospitalization due to lumbar disc herniation. International Archives of Occupational and Environmental Health. (2018) ;91: (6):689–94.11. |
[4] | Burström L , Nilsson T , Wahlström J . Whole-body vibration and the risk of low back pain and sciatica: a systematic review and meta-analysis. International Archives of Occupational and Environmental Health. (2015) ;88: (4):403–18. |
[5] | Mayton AG , Kittusamy NK , Ambrose DH , Jobes CC , Legault ML . Jarring/jolting exposure and musculoskeletal symptoms among farm equipment operators. International Journal of Industrial Ergonomics. (2008) ;38: (9-10):758–66. |
[6] | Blood RP , Rynell PW , Johnson PW . Whole-body vibration in heavy equipment operators of a front-end loader: Role of task exposure and tire configuration with and without traction chains. Journal of Safety Research. (2012) ;43: (5-6):357–64. |
[7] | ISO. Mechanical Vibration and Shock: Evaluation of Human Exposure to Whole-body Vibration. Part 1, General Requirements: International Standard ISO 2631-1:1997 (E). ISO; 1997. |
[8] | ISO/TR. Earth-MovingMachinery - Guidelines for Assessment of Exposure to Whole-Body Vibration of Ride-on Machines - Use Harmonized Data Measured by International Institutes, Organizations and Manufacturers. Technical report. ISO/TR 25398:2006 (E). ISO/TR; 2006. |
[9] | Micromega Dynamics SA. www.micromega-dynamics.com. [Online].; 2016 [cited 2019 09 17/09/2019. Available from: https://micromega-dynamics.com/wpcontent/uploads/2016/08/VibWork-Whole-Body-Vibration-Dosimeter.pdf. |
[10] | Caruel E , Donati P , Lebrech A . www.inrs.fr. [Online].; 2012 [cited 2019 09 17/09/2019. Available from: http://www.inrs.fr/media.html?refINRS=ED%206130. |
[11] | Danem. www.danem.fr. [Online].; 2017 [cited 2019 09 17/09/2019. Available from: http://bo.danem.com/wiasp/onlineguides/fr/businessobjects report format.pdf. |
[12] | Directorate-General for Employment, Social Affairs and Inclusion (European Commission). www.publications.europa.eu. [Online]. [cited 2019 09 17/09/2019. Available from: https://publications.europa.eu/en/publication-detail/-/publication/3f9392ff-8975-4139-9ea2-5b168a334664. |
[13] | Alphin MS , Sankaranarayanasamy K , Sivapirakasam SP . Experimental evaluation of whole body vibration exposure from tracked excavators with hydraulic breaker attachment in rock breaking operations. Journal of Low Frequency Noise, Vibration and Active Control. (2010) ;29: (2):101–10. |
[14] | Chaudhary DK , Bhattacherjee A , Patra AK , Chau N . Whole-body vibration exposure of drill operators in iron ore mines and role of machine-related, individual, and rock-related factors. Safety and Health at Work. (2015) ;6: (4):268–78. |
[15] | Coggins MA , Van lente E , Mccallig M , Paddan G , Moore K . Evaluation of hand-arm and whole-body vibration in construction and property management. Annals of Occupational Hygiene. (2010) ;54: (8):904–14. |
[16] | McCallig M , Paddan G , Van Lente E , Moore K , Coggins M . Evaluating worker vibration exposures using self-reported and direct observation estimates of exposure duration. Applied Ergonomics. (2010) ;42: (1):37–45. |
[17] | Motmans R . Reducing whole-body vibration in forklift drivers. Work. (2012) ;41: (Supplement 1):2476–81. |
[18] | Tiemessen IJ , Hulshof CT , Frings-Dresen MH . An overview of strategies to reduce whole-body vibration exposure on drivers: A systematic review. International Journal of Industrial Ergonomics. (2007) ;37: (3):245–56. |
[19] | Kim JH , Marin LS , Dennerlein JT . Evaluation of commercially available seat suspensions to reduce whole-body vibration exposures in mining heavy equipment vehicle operators. Applied Ergonomics. (2018) ;71: :78–86. |
[20] | Okunribido OO , Magnusson M , Pope MH . The role of whole-body vibration, posture and manual materials handling as risk factors for low back pain in occupational drivers. Ergonomics. (2008) ;51: (3):308–29. |
[21] | Raffler N , Rissler J , Ellegast R , Schikowsky C , Kraus T , Ochsmann E . Combined exposures of whole-body vibration and awkward posture: a cross sectional investigation among occupational drivers by means of simultaneous field measurements. Ergonomics. (2017) ;60: (11):1564–75. |
[22] | Langer TH , Iversen TK , Andersen NK , Mouritsen OØ , Hansen MR . Reducing whole-body vibration exposure in backhoe loaders by education of operators. International Journal of Industrial Ergonomics. (2012) ;42: (3):304–11. |